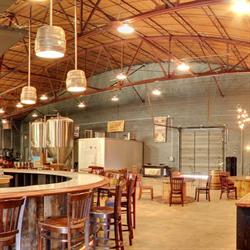
The most important part of the brewery steam system design is to size the boiler properly. An oversized boiler can result in frequent cycling while an undersized boiler may never be able to meet the temperature requirements of the brewery. Both of which will adversely affect the brewing process. A steam boiler should be sized according to the connected load. The connected load includes all the vessels and tanks as well as the piping. The manufacturer of the brewing equipment should provide the Btu consumption of their equipment. Another sizing consideration is the planned expansion of the brewery. Since the market of brewing and distilling is growing, the boiler you design today may be undersized next year. If you do an internet search, there are many rules of thumb for sizing a brewery boiler including:
50,000 Btuh per barrel of capacity,1-2 Boiler HP (BHP) per brew barrel,1 BHP per barrel for smaller brewers and 2 BHP for brewers per barrel with large hot liquor tanks. As with most rules of thumb, they may or may not be accurate for the facility. According to brew industry design expert, Blaine Clouston the equipment manufacturers generally ensure the heating equipment to meet the following:
Brewkettle heating - 1.5 degree F/minute
Brewkettle, evaporation - 5- 6%/hr
Mash Vessel Heating - 1.5 degree F/minute
Hot Liquor tank - ability to heat water 1.5 times the brewhouse size in 4 hours. Example; a 10 barrel system would typically use up to 15 barrels in hot liquor.
Based on his extensive engineering background, Mr. Clouston has some shortcuts which he feels are more accurate for sizing:
Brewkettle Heating and Boiling = 32,000 Btu/Hr/bbl
Hot Liquor Heating from 60-175F in 4 hours = 19,500 Btu/Hr/bbl
Mash Vessel Heating = 29,000 Btu/Hr/bbl
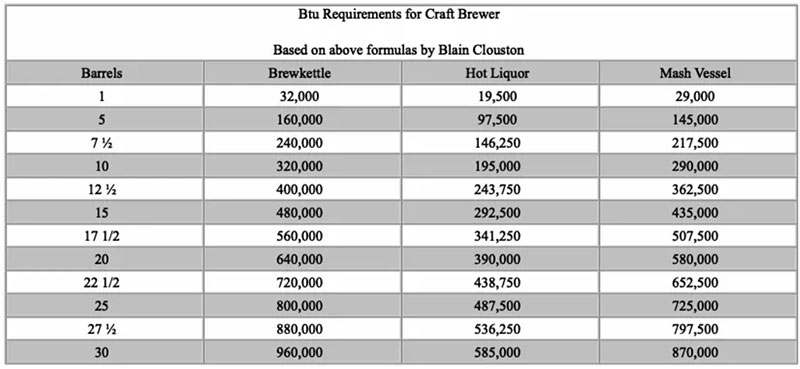